Given the COVID-19 pandemic, workplaces across the globe implemented restrictions that were designed to keep people safe. For BHP, a leading mining company, these restrictions affected their operations as they are unable to fly people to and from its mine sites as freely as it did before. Regardless, their equipment would still need to be inspected, serviced and maintained.
In order to ensure the smooth running of their operations, BHP increased the pace of innovation during the pandemic with strong support from its partnership with Microsoft.
One of which was through the use of mixed reality in its day-to-day operations to keep their people safe, and their productivity up. Dash Maintainer Tools, developed by BHP’s maintenance and innovation teams, allow front line personnel to securely collect data from machinery remotely, avoiding the potential risks associated with manually checking dials or taking readings from heavy mobile equipment.
Leveraging IoT sensors and industrial computers connected to Azure, the Dash solution gets data into the hands of maintenance technicians on their smartphone or tablet.
Staying safe during COVID-19
BHP introduced many rigorous measures and controls to reduce the risk of transmission – including limiting numbers at its mine sites to only those required to enable safe operations while those who able to work from home.
Originally, this meant being unable to get the relevant workers to keep developing the Dash tools at the same speed nor fly multiple experts to a mine to set up new equipment, solve a problem, or conduct an inspection.
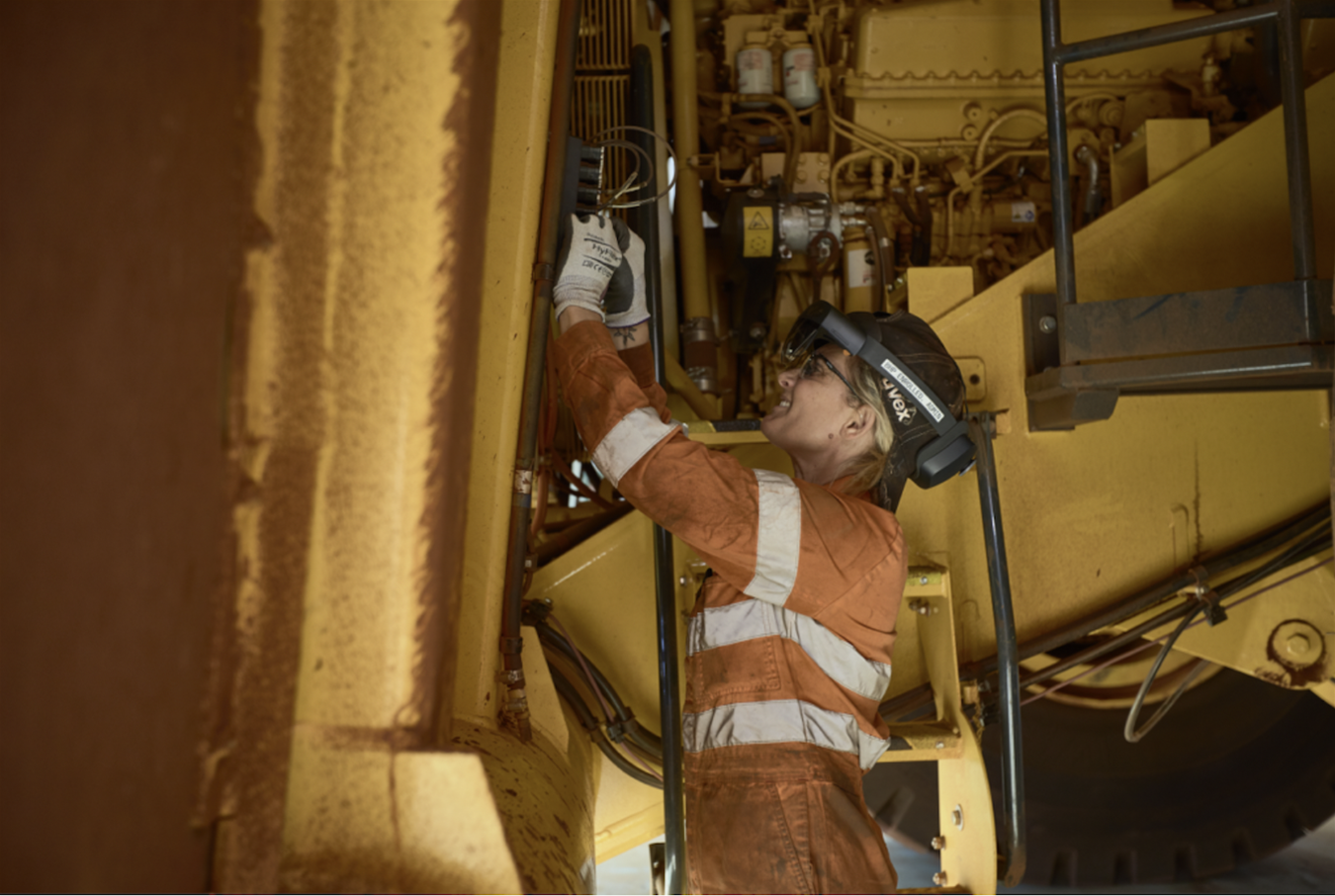
Through the use of HoloLens and mixed reality working in tandem with Dynamic 365 Remote Assist, BHP managed to deliver the expertise of the relevant workers virtually to the teams still working at BHP’s Pilbara operations at Western Australia to support continued development of the Dash Maintainer Tools.
Intuitive solution
The trials of the HoloLens2 at the Innovation Centre Lab that the BHP team ran with their experienced mechanical fitter helped them to fine tune how the system would be used, and making sure that people using it stayed safe.
After the initial trial and test of the system, it was used to support the planning and installation of the Dash Maintainer Tools product on a 300 tonne Komatsu dump truck. The experts were in Perth while a mechanical fitter and an auto-electrician actually installed the IoT system onsite.
“A guiding principle for me around any new technologies or tools is that if someone needs to refer to a user manual, then your design isn’t good enough. This is key for providing the best support possible to our teams at site, especially during this time,” said Alex Bertram, Digital Products Manager at BHP.
As a testament to that principle, the site team at Pilbara, without a manual or formal training, managed to effectively operate the HoloLens2 with just a bit of phone support.
This demonstrated the power of the HoloLens2 and Dynamics 365 Remote Assist which forms the technical foundations of the solution used by BHP.
Digital transformation for BHP
BHP saw the opportunity for the solution to tackle the immediate challenges posed by COVID-19 travel restrictions – but also expose onsite mine personnel to leading edge technology that could have long term benefits for the company.

According to Kim Horton, BHP Field Maintenance Superintendent, “I’ve never seen people so excited – having a tool that enables them to do multiple things across different areas. To put a schematic in front of someone from a maintenance perspective, from the other side of the world or 1600 km away in Perth, to help enable them.”
The deployment of mixed reality technology has the potential to be rolled out more widely, and deliver safety and productivity benefits long after COVID-19 abates. Moreover, there is further scope in making the physical delivery of equipment to sites more efficient.
“This technology can help us reduce the time and cost associated with regular travel, increase the speed of maintenance and new equipment deployment without compromising safety, and support greater inclusion and diversity,” said Bertrand.
Having seen the HoloLens2 solution’s potential, BHP has run further trials across its rail workshops and maintenance teams in Perth and the Pilbara, and at several other global locations in Australia, the US and Chile.